Your cart is currently empty!
BLOQUES DE HORMIGÓN REALIZADOS CON NEUMATICOS RECICLADOS
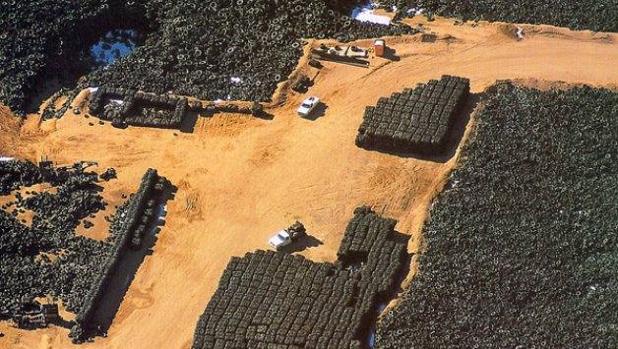
Una compañía estadounidense propone dar un nuevo uso a los neumáticos usados, convirtiéndolos en bloques de hormigón combinados con neumáticos reciclados. Con esta combinación de materiales consiguen un producto que puede servir para levantar bloques de contención, de las laderas, protecciones de las pendientes, diques para el control de las inundaciones, e incluso cimientos de edificios. La empresa, llamada Recycling PMGI, indica que necesita entre 20 y 40 neumáticos para producir un bloque.
El proceso de fabricación de los bloques de hormigón realizados con neumáticos usados es similar al de fabricación de los bloques de cemento con plásticos reciclados. El llamado «conglomerante» es el cemento al que se añaden aditivos que mejoran sus características físicas a la vez que supone un ahorro en la cantidad de hormigón o cemento necesario en la mezcla.
Los neumáticos se fabrican a partir de caucho natural, caucho sintético y otras sustancias como cables, textiles y demás productos químicos. Su posterior proceso de reciclaje resulta muy costoso.
En España se aprobó el Real Decreto 1619/2005 sobre gestión de neumáticos fuera de uso, que prohibe arrojarlos en los vertederos desde julio de 2006. En esa fecha varios fabricantes de cubiertas crearon Signus que, además de recoger y reciclar los neumáticos, realiza un trabajo de clasificación previo a su salida al mercado para hacer un seguimiento de todos los neumáticos que se venden.
Así, cuando los consumidores entregan sus neumáticos usados en el taller, este debe solicitar la recogida de los mismos para que los trabajadores de Signus los depositen en las plantas de clasificación de neumáticos. Una vez ahí, los expertos separan los que pueden ser reutilizables, para su posterior venta como productos de ocasión; de los que ya no tienen más vida útil, que se envían a las instalaciones de transformación.
Una vez que llegan a estas plantas de reciclaje pueden seguir dos procesos de transformación. O bien se trituran una vez sin separar los distintos componentes –textil, acero y caucho– y se convierten en productos derivados; o se realiza un segundo tratamiento para separar los compuestos y darles una segunda vida con distintas aplicaciones como el relleno de los campos de césped artificial, las losetas de los parques infantiles o las barreras de hormigón de la mediana de las autovías. La mayor parte, más del 60%, se destina a la separación de sus componentes, acero, caucho y textil, para reciclarlos en diferentes aplicaciones. El resto se destina a triturado. El triturado de cementera se utiliza con dos fines. Porque el cemento necesita hierro y sílice, y estos materiales constituyen el 25% del neumático, que se queda en el cemento (coprocesado). El 75% del material de los neumáticos es caucho, con gran poder calorífico, y parte de ese caucho es natural, y por tanto es biomasa renovable, una muy buena materia prima.
fuente: www.abc.es